Selection Principle and Applications of Different Strainers
On this page
Strainers are essential in industrial fluid systems, safeguarding equipment from wear and blockages by removing solid particles, ensuring uninterrupted process flow and consistent product quality. As industrial technology advances, strainers evolve to meet diverse industry needs. This article outlines strainer selection principles, covering diameter, pressure rating, mesh size, material selection, and pressure drop. It offers practical guidance for engineers to choose the best strainers for efficient and cost-effective filtration.
Selection is a critical step in strainer application, directly impacting filtration efficiency and equipment performance. Correct selection involves considering fluid characteristics, process requirements, and operating conditions to ensure strainers operate efficiently and reliably.
The inlet and outlet diameters of strainers should match the inlet diameter of the associated pump and generally align with the diameter of the inlet piping to ensure smooth fluid flow.
The pressure rating of strainers should be determined based on the maximum pressure expected in the strainer pipeline to ensure stable operation under various conditions.
The choice of mesh size depends on the size of impurities that need to be intercepted, tailored to specific requirements of the medium's process flow. Different specifications of screens can intercept particle sizes, as detailed in a referenced "Mesh Specifications" table.
Strainer materials typically match those of the connected process pipelines to ensure overall system compatibility. Depending on service conditions, materials such as cast iron, carbon steel, low-alloy steel, or stainless steel can be selected as needed.
For water strainers, pressure loss typically ranges from 0.52 to 1.2 kPa under rated flow conditions, a critical parameter for evaluating strainer performance.
Different types of strainers are suitable for various industrial scenarios, designed and manufactured according to medium characteristics and process requirements to meet specific filtration needs.
Widely used in pipelines for various media such as steam, air, water, and oils, stainless steel strainers effectively protect equipment such as pumps and valves from blockages and damage caused by rust, welding slag, and other impurities. They are known for their corrosion resistance, easy drainage, large filtration area, low pressure drop, simple structure, compact size, and light weight, with strainer mesh materials offering long service life.

Essential filtration devices in pipeline systems, Y-type strainers are typically installed at the inlet of pressure reducing valves, pressure relief valves, level control valves, or other equipment to remove impurities from the medium, ensuring the normal operation of valves and equipment. They are favored for their simple structure, low resistance, and convenient drainage.
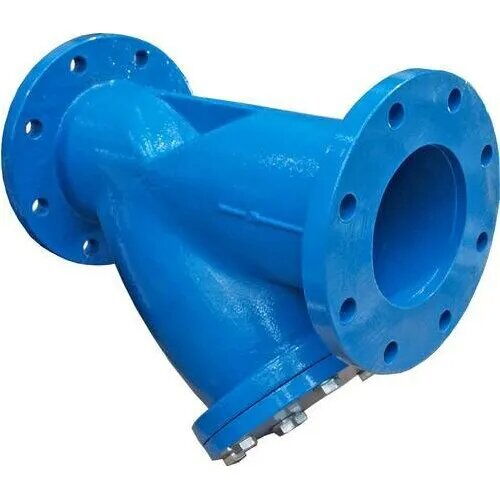
Used to remove small amounts of solids from liquids, basket strainers protect compressors, pumps, and other equipment and instruments, ensuring their normal operation. They are crucial for improving product purity and purifying gases, widely applied in industries such as petroleum, chemical, synthetic fiber, pharmaceuticals, and food. Basket strainers consist of a housing, drainage cover, filter core, screen, bolts, and other components.
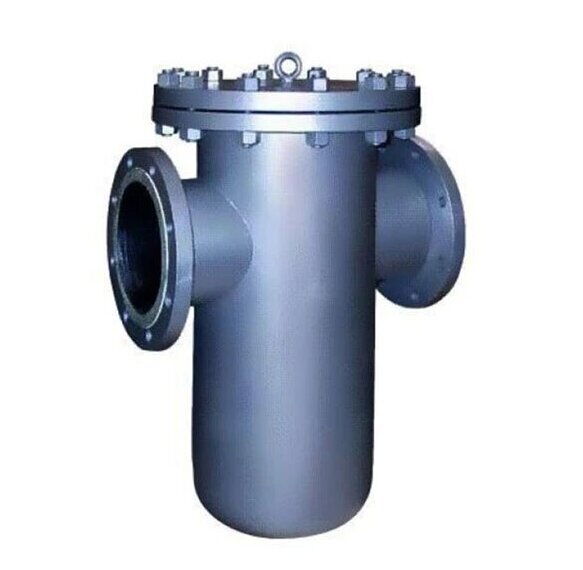
Similarly applied in pipelines for various media, T-type strainers protect pipeline systems from blockages and damage caused by impurities. They feature strong anti-pollution performance, easy drainage, large flow area, low pressure drop, simple structure, small size, and stainless steel strainer mesh with high corrosion resistance and long service life. T-type strainers are available in straight-flow and diverting-flow types, with mesh densities ranging from 10 mesh to 120 mesh, operating temperatures from 0°C to 450°C, selectable according to user requirements.
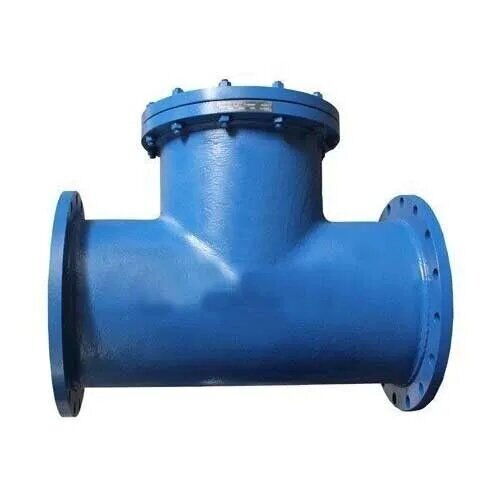
Correct strainer selection is crucial for ensuring the efficient operation of industrial systems. By following the above selection principles and choosing the appropriate strainer type based on specific application scenarios, maximum strainer performance can be achieved, protecting equipment, extending service life, and enhancing overall system reliability.